Differences between HDPE corrugated and concrete pipes. Why choose corrugated pipes.
“Flexible” pipes (made of PE, PP, PVC and HDPE) are able to satisfy all the initial project needs in a more efficient manner due to the thermoplastic material characteristics. These characteristics can easily solve general work site problems because they are durable, chemically resistant and last but not least, easy to handle.
The “rigid” ones instead (made of concrete, iron and stoneware) can offer a good static performance but they lose in durability, chemical resistance and being heavy demand more manipulation thus increasing installation costs.
The main differences that can be noted between HDPE pipes and those built in concrete are:
- BUILDING TECHNOLOGIES
For the production of concrete pipes, rustic mold are used, vibrated or spun; while HDPE corrugated pipes production is made with highly technological machinery, using also sophisticated control system, able to manufacture pipes in different lengths requested by the customer;
- PHISICAL CHEMICAL CHARACTERISTICS
The concrete pipes are extremely heavy. They have a good axial resistance but a poor traction resistance.
Let’s consider also a durability lower than 50% with respect to a normal corrugated HDPE conduit that is also lighter and present an excellent impact resistance. HDPE offers also an elevated resistance against aggressive chemicals. Life durability of the HDPE pipes is estimated in periods superior to 50 years;
- HYDRAULIC CALCULATIONS
HDPE presents a wall abrasion notably reduced in comparison with the concrete pipe. This characteristic consents.
- Increase of the fluids velocity inside the pipe, maintaining the same pipe capacity;
- Less risk of sedimentation and minor frequency of maintenance;
- Lower interior diameter needed, since the maximum capacity of the project can be satisfied with a lower conduit capacity: this leads to lower costs and reduced time of realization of the project;
- Environmentally friendly impact.
Example 1
Drainage pipeline construction which satisfies maximumj capacity (Qmax) equal to 1350 l/sec.
tab. 1
PIPES
DN 1.200 |
CAPACITY
Q [ l/sec. ] |
FULL capacity speed |
V [ m/sec. ]
HDPE Corrugated |
DN = d.e. (d.i. = 1030
mm) |
1350 | 77% | 1,95 |
CONCRETE (d.i.) | 1350 | 71% | 1,57 |
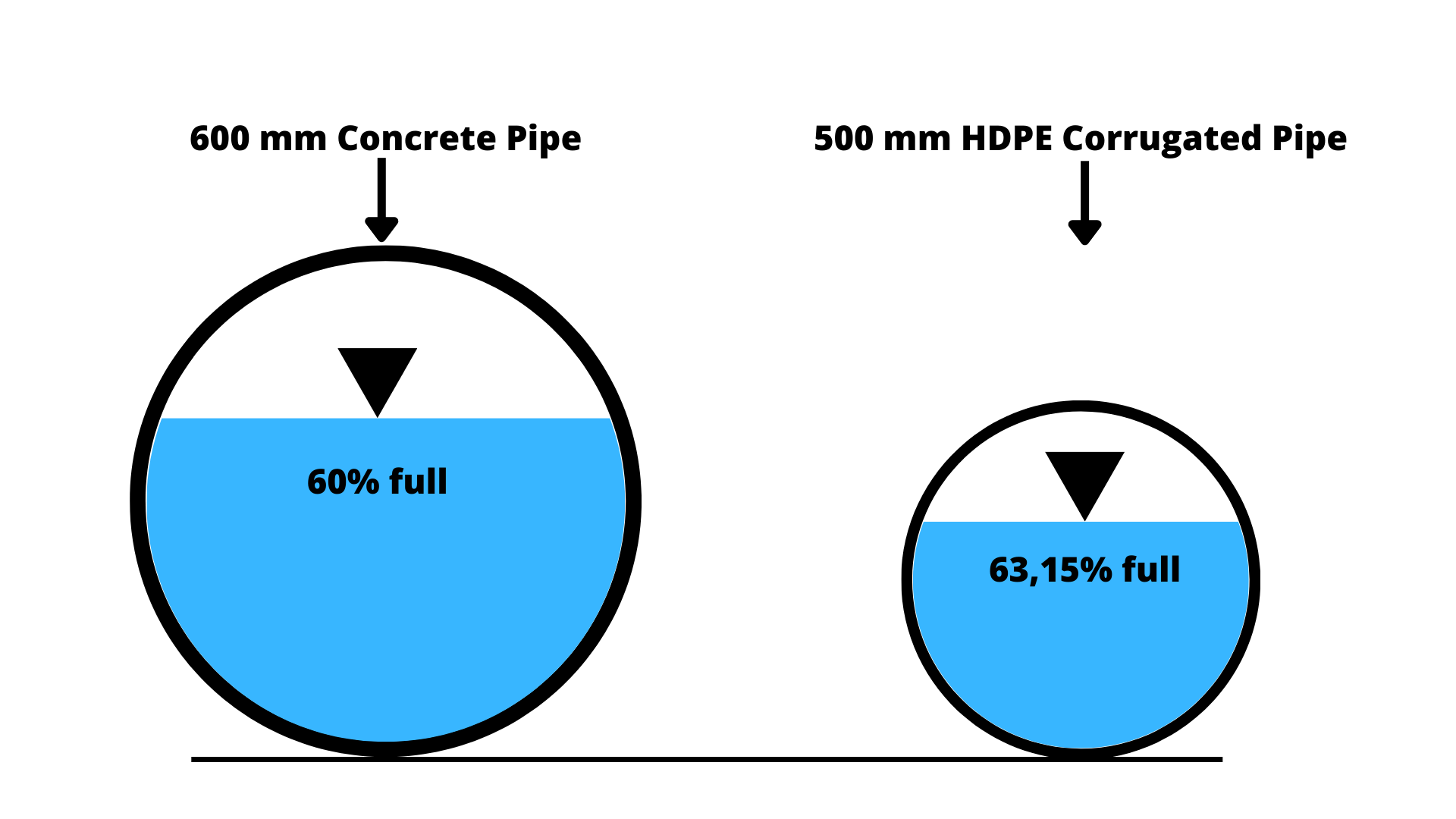
Example 2
Drainage pipeline construction which satisfies maximum capacity (Qmax) equal to 1295 l/sec.
tab. 2
PIPE
DN 1.000 |
CAPACITY |
FILLING
Q [ l/sec. ] |
SPEED
V [ m/sec. ] |
Corrugated PEHD
DN = d.e. (d.i. = 852 mm) |
800 | 76% | 1,82 |
CONCRETE (d.i.) | 800 | 69% | 1,38 |
The capacity of the system designed with concrete pipe parameters can be equally satisfied with HDPE corrugated pipes of equal diameters.
- CHEMICAL CORROSION RESISTANCE and ABRASION RESISTANCE
Concrete conduits can be taken into consideration when the waters are clear. They are less indicated for industrial wastewater, while HDPE chemical resistance, in relation to the major corrosive chemical composites, can be defined as excellent. Concrete is generally “hard” and therefore “fragile”: there are test results that prove the concrete pipe lasts shorter time, therefore the material has a reduced abrasion resistance. On the other hand, HDPE pipes, thanks to the low elasticity module and the reduced roughness, have an elevated abrasion resistance.
- MOVEMENT AND LAYING
From the weights on table tab. 3 you can clearly see that it is necessary to utilize bigger and more powerful tools which are therefore more costly. The major length of the HDPE pipes guarantee a speedier laying together with an higher work-site productivity.
tab. 3
Pipes | In pallet of |
DN 1000
q/bar |
Dn1200
q/bar |
HDPE corrugated
Pr EN 13476-1 SN4 |
6m | 2.28 | 3.3 |
VIBRATED concrete | 2m | 26.85 | 38.05 |
Differences | 1→ 3 | +1077% | +1053% |
Weighted average: concrete+ 1065% per bar (≡ 3396% al m)
The major length of the bars, reduces also the number of junctions (6 times inferiors), with a significant reduction of critical points and therefore reduced costs for the safety.
For HDPE corrugated pipes, the preparation of an adequate trench bed is necessary: the pipes should have an adequate isolation against those materials, which could cause stress.
The flexible pipes are highly adaptable to terrain movements, and they easily support earth movements without interrupting the flow.
In the end why choose the HDPE.
To optimize the entire network, it is necessary to have high performances in the operability of the entire system.
The choice must not only be concentrated on the material, but also on the entire system. Overall, if we consider the single element, a network composed of concrete material offers a minor cost with respect to the HDPE corrugated pipe; but in reality, it is necessary to consider the minor efficiency in whole system due to:
- Minor chemical and biological resistance of the concrete product;
- Minor adaptability to the soil movements;
- Minor durability;
- Minor hydraulic efficiency;
- Major maintenance.
Therefore, a modern network made by polyethylene elements (pipes, fittings, special pieces and manholes) has an added value which has no equals, especially considering the total costs in addition to high safety.