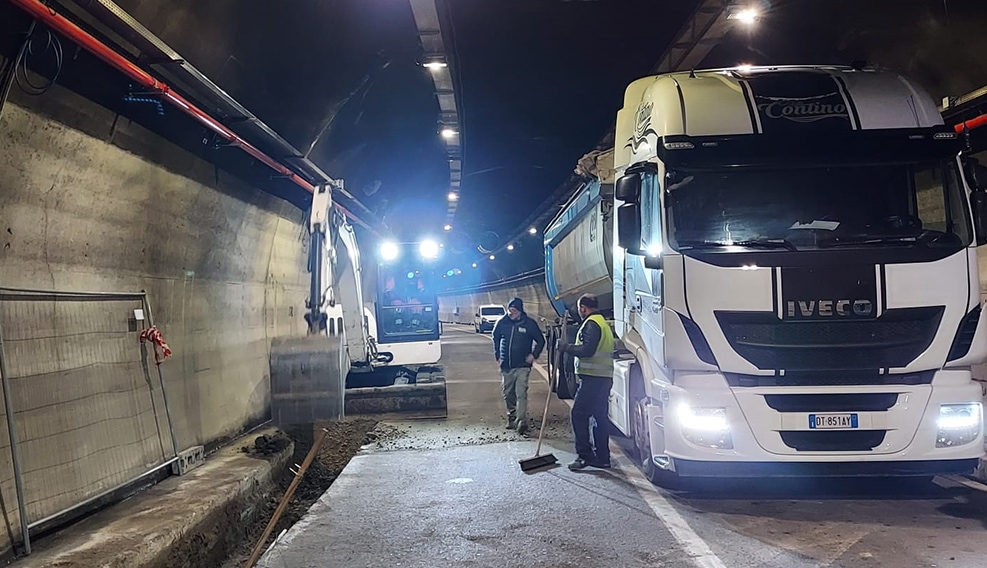
SAFE TUNNEL WITH ” NO FIRE” DRAINAGE SYSTEM
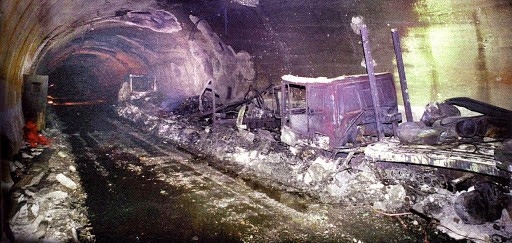
THE PRINCIPLE OF OPERATION
It consists in creating an impediment to the entry of air (oxygen) inside the collector, in order to quickly stop the combustion of flammable liquids inside it in case of fire. This is achieved by creating with water, by difference in density, a barrier to air entry. The material used for the construction of the NO FIRE is polyethylene (PE), in self-extinguishing class “V2” (certified with tests at accredited third laboratories).
The installation of the NO FIRE system (storm drain plus pipes) provides that, mainly due to the mandatory surface area of installation, the whole system is statically protected by a total reinforcement of concrete.
Therefore, the NO FIRE system also automatically acts as a disposable formwork of the contour conglomerate that, in case of fire and possible damage to the plastic part, will allow the system to maintain its geometric conformation and therefore its operation
Any damage implies the subsequent removal and replacement that, most likely involve a wider arrangement, or even reconstruction, of the section of the tunnel regardless of the state of the elements of the drainage system.
NO-FIRE SR “superribassata” (super-low)
Returning to our case, as mentioned, the choice fell on the NO-FIRE SR channel classified V2, which is used in tunnels where the reverse arch does not allow to have too deep excavations.
It consists of two parts:
- The upper part is a 100% virgin LLDPE roto-moulded channel on which a D400 ductile iron grid is installed. In addition, there are two caps in PP DE= 125 m to ensure inspection.
- The lower part is a LLDPE roto-moulded siphon, which allows the creation of isolated compartments between the branches of the collector and the tunnel environment. The upper part is inserted in the lower part by means of appendices that can be cut to size making it in fact telescopic. The “NO-FIRE” channel can be connected to the collector by means of the DE= 250 mm corrugated pipe cups.
Another decisive element for the choice of this solution was represented by the homogeneity of the system, being channels and pipes both in plastic material.
Moreover, given the low coverings and the possible presence of potential aggressive liquids, a pipe like HYDRO 16 was needed that combined greater resistance to crushing (SN 16) and greater resistance to chemical agents.
This post is also available in: Italian