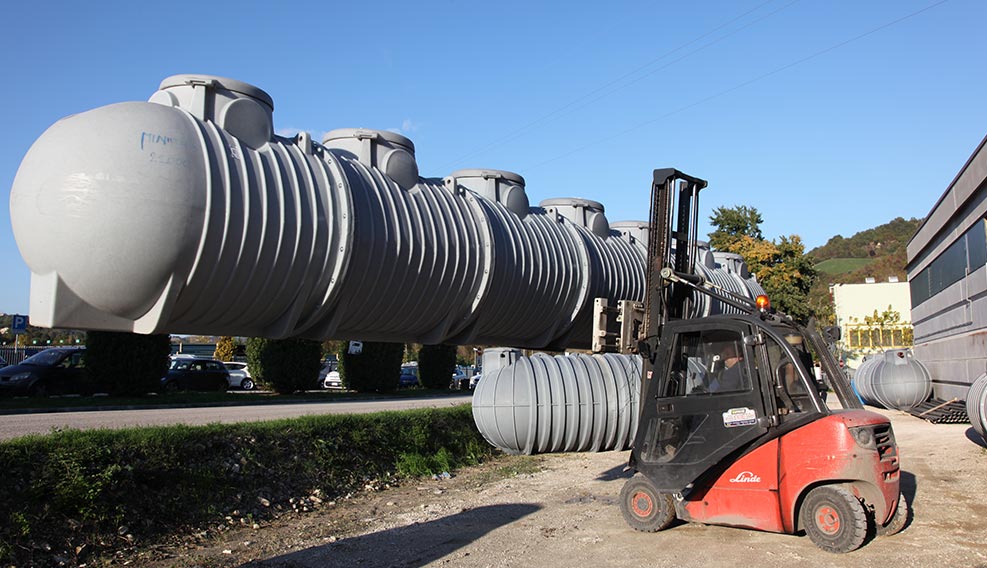
Advantages of pe tanks made through rotational moulding
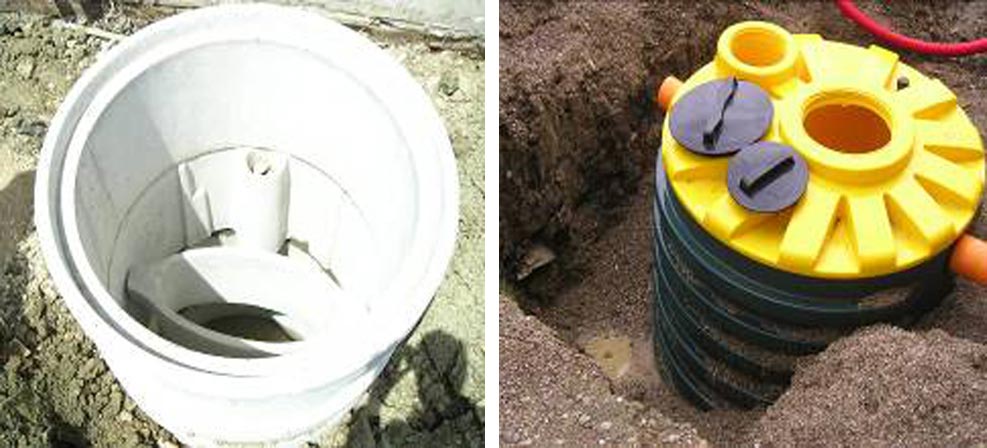
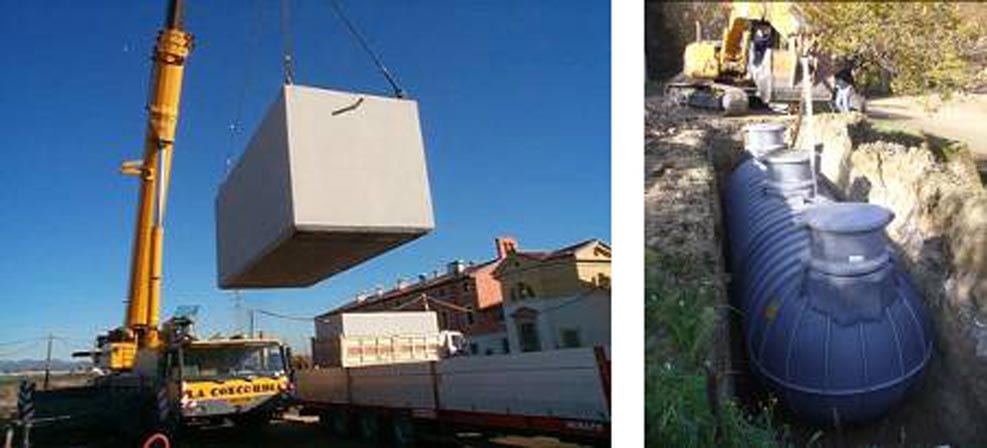
Concrete and PE tanks transport
Polyethylene has zero environmental impact because is 100% recyclable, thus allowing the material to be reused for the manufacturing of new products. There are no disposal cost.
LONG SERVICE LIFE
The concrete products placed on slabs (reinforced or not reinforced) and drowned in reinforced ready mix are usually not affected by the chemical actions produced by the surrounding ground. It is not the same result for those products that are placed in common or chosen ground. Obviously the more the mix is porous the less chances of chemical aggression we have. Concrete products allows the creation of organic and biochemical concretions and the resistance to alkalis and acids is very low.
There is the creation of a thin mucous layer due to the surfaces’ wetness of the concrete tank containing waste water. On this layer the biological activities are at their highest and the anaerobic conditions allow the sulphate reduction and the creation of sulphide. Between the mucous and sewage layers there is the creation of an aerobic space (with oxygen). The hydrogen sulphide (H2S) is a well known gas, especially for its smell (similar to the rotten eggs one), which forms in presence of organic material decomposition, particularly in the albumin (the white part of eggs) which releases huge H2S quantities. The H2S that comes out as gas from the solution, can lead to the oxidation of fixed surfaces. In presence of humidity, the H2S becomes sulphuric acid through a bacteria (Thiobacillus Concretivorus) and causes corrosion on the surfaces. Various inner coating of concrete products revealed the material cost increase and the following issues:
On one hand, the coating made with stoneware briquettes requires more grouting operations with suitable materials. These operations are needed because the corrosive and abrasive actions between two briquettes pointed out their detachment. The coating with epoxide resin is made with reduced thicknesses and with resins with no shock absorption capacity (loading, transport, unloading, on-site handling, laying and connection) which cause cracks and detachment from the walls. These situations implement the corrosive phenomena, which lead to uncertain effectiveness.
On the other hand, the PE chemical resistance is excellent and it can survive the majority of corrosive chemical compounds and solvents. This is possible because PE is inert in those application fields such as sewerage, especially in the industrial one.
PE is 100% resistant to electrochemical and biological corrosion. There is no need for coating and no risk of damage or detachment from walls (usually PE finds application as outer and/or inner protection of other products).
MATERIAL QUALITY
- PE is a non-toxic material, this means that the products can hold drinking water and various fluids for human consumption (milk, wine etc.). Thanks to this feature, the PE inner surfaces do not require specific resins or other materials.
- Anti UV additives are added in the PE that finds application in the tanks manufacture. These additives cancel the sun impact on the tank allowing the products to be unbreakable.
- The items are manufactured as single pieces without welding points. This is what guarantees an high level of toughness and strength.
- PE elasticity ensures an excellent tolerance to earthquakes. The concrete toughness and fragility allows the creation of cracks.
- PE products have inner smooth surfaces. The smoothness allows a full cleaning and the pores absence minimizes the growth of algae and bacteria.
This post is also available in: Italian